Technologies that have traditionally been used in fixed installations to detect hydrocarbon gas leaks, like IR Open Path Sensors and Catalytic/IR Point Sensors all have one restriction: in order to detect a leak, the gas itself must either be in close proximity to the detector or within a specified area. Traditional gas detection systems frequently fail to detect the gas, as the gas does not reach the detector due to unfavorable outdoor environmental conditions like quick dispersion of the gas cloud from a leaking outdoor installation and changing wind directions.
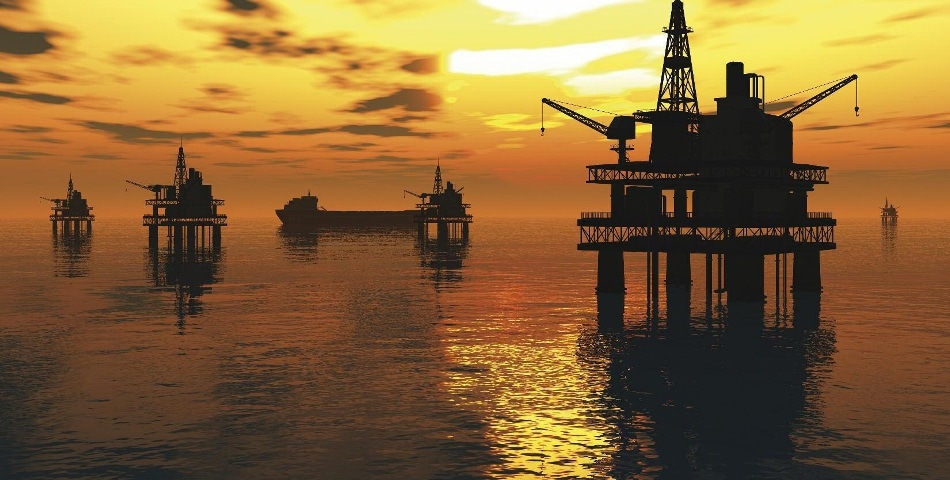
GM Ultrasonic Gas Leak Detectors make use of powerful microphone technology. The noticeable high frequency ultrasound radiated by all high pressure gas leaks is detected by the detectors while sensing outdoor leaks. With the unique Gassonic ultrasonic sensing technology, it is possible to detect gas leaks not because of the leaking gas reaching the sensor but merely because of the sound of the gas leakage.
GM Ultrasonic Gas Leak Detectors enable lower operation costs and quicker response times.
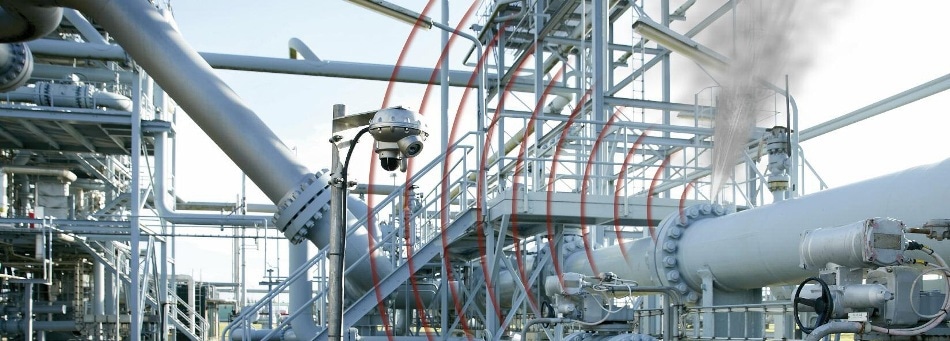
Significantly Increased Safety
Operators in the petrochemical sector are continuously looking for ways to avoid loss, minimize risk, and guarantee safe and reliable production. Speeding up the response time of the Fire & Gas Detection System is one of the key elements in attaining this and increasing the overall efficiency.
The Gas Release Event Tree shown below puts the effects of a gas leak into perspective. It is clear that the utilization of suitable technology to sense hazards early (initiation), before they develop or escalate has a significant impact on major accident risk reduction.
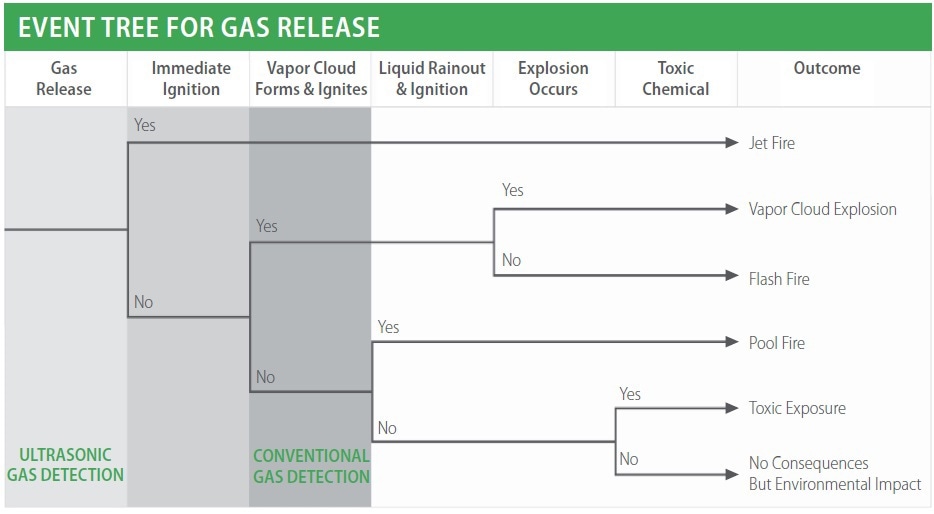
The gas release event tree illustrates the sequence of events that can take place in the event of a gas release. The figure shows that UGLD responds at gas leak initiation whereas conventional detectors only respond when the gas has accumulated and formed a vapor cloud.
Traditional gas detection systems have to wait for the gas to become a vapor cloud, which may or may not ignite, and which may or may not permit loss prevention by allowing the gas facility to shut down on time. Ultrasonic Gas Leak Detectors (UGLD) can detect gas leak at the speed of sound, without being affected by dilution of the gas and changing wind directions (see graphic shown below).
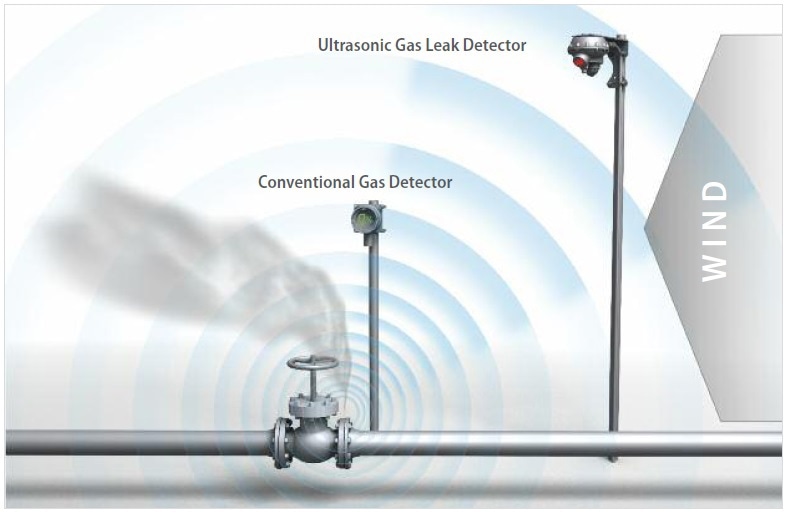
Ultrasonic gas leak detectors do not need physical contact with the gas. They are unaffected by wind, gas dilution and the direction of the gas plume.
What is Ultrasound?
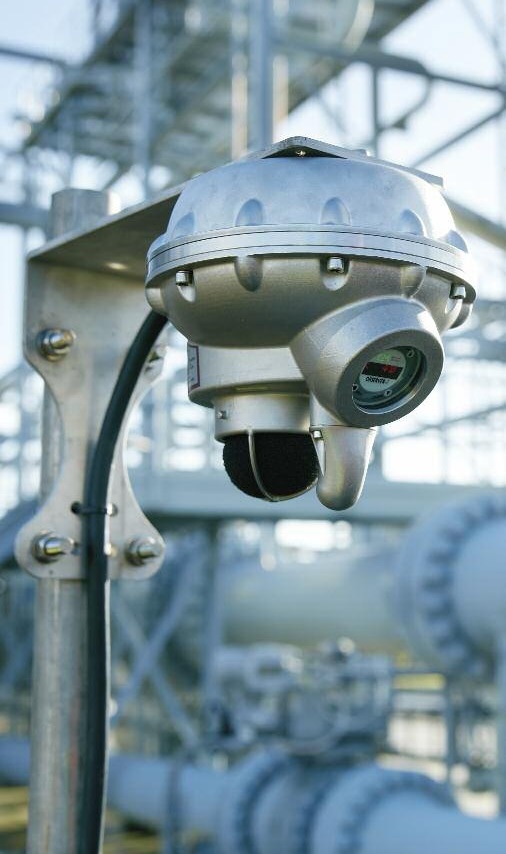
A sound wave is just a pressure pulse in the air, which is detected by the human ear the same way that it is detected by a microphone. The human ears can only hear acoustic sound waves in the frequency ranging between 20 and 20,000 Hz (20 kHz) and hence the name audible frequency range. Ultrasound refers to acoustic sound frequencies above 20 kHz.
The hissing sound produced by a pressurized gas released during a leak is called broad band acoustic noise, which ranges between the audible frequency range and the ultrasonic frequency range. Ultrasonic Gas Leak Detectors of yesteryears only “listened” for the gas leak noise in the ultrasonic frequency range from about 25 kHz and above, but by using the new Artificial Neural Network sound algorithms in the OBSERVER-i, the detector’s frequency range can be brought down to 12 kHz without taking in unwanted background noise. The lower frequency range increases the detection radius of the OBSERVER-i significantly in all application areas compared to previous versions of Ultrasonic Gas Leak Detectors while still maintaining false alarm immunity.
Human Hearing vs. Ultrasound
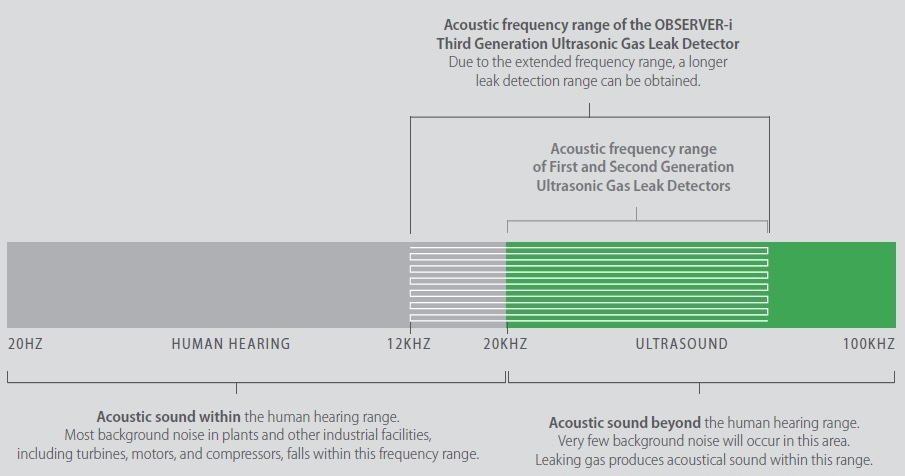
SENSSONIC Acoustic Self-Test Technology
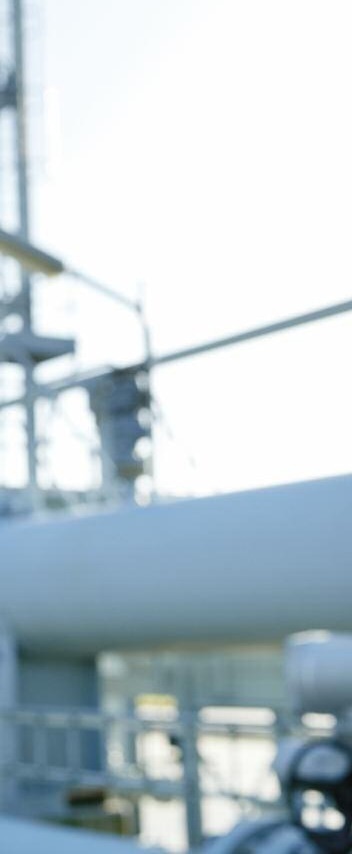
In field instrumentation, especially in rough outdoor environments, breakdowns or faults may occur. It is unacceptable if such breakdowns or faults involving safety are left undisclosed. To meet the challenge of ensuring failsafe operation for the most sophisticated Ultrasonic Gas Leak Detectors, the SENSSONIC self-test technology has been developed.
The SENSSONIC self-test technology gives a full acoustic integrity test of the OBSERVER-i Ultrasonic Gas Leak Detector every 15 minutes through a high-quality sound transducer sending an air-borne ultrasonic signal to a microphone system equipped in the detector. This makes sure that the electronics and the microphone are tested constantly within well-defined tolerances. Moreover, the operator is warned if the detector fails this standard test.
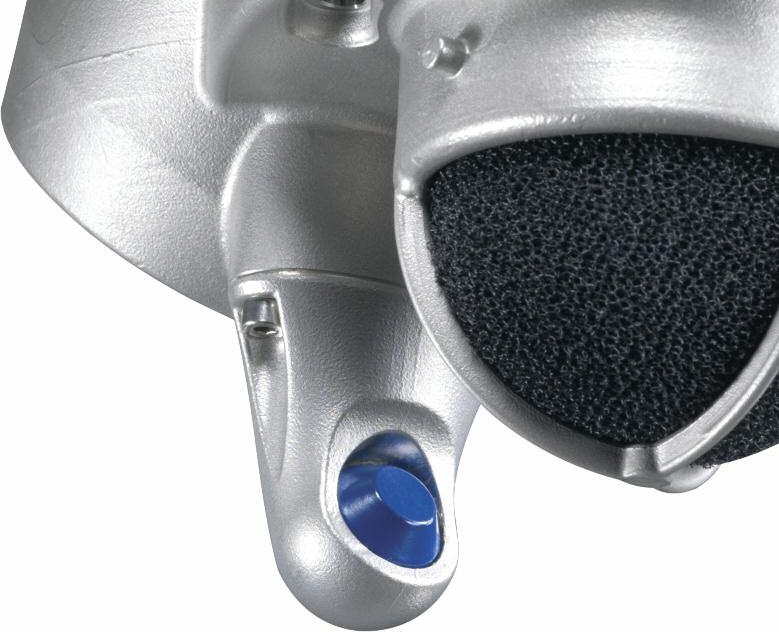
Reliable and failsafe operation of the GM Ultrasonic Gas Leak Detectors is ensured by the SENSSONIC technology, which helps ensure human safety in an industrial facility and guard one’s possessions.
The SENSSONIC technology is the only technology available in the market to self-test both the microphone system and the protective windscreen protecting the microphone. This ensures that dirt and other contaminants on the detector wind screen, that could decrease leak detection performance, will be detected.
Why Neural Network Technology?
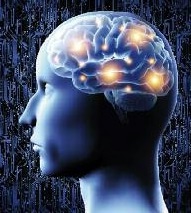
An important performance parameter for an Ultrasonic Gas Leak Detector is to make sure high acoustic sensitivity to real gas leaks over a wide area and simultaneously reducing the interference from background noise sources that are not associated with gas leaks. To overcome the interference, first and second generation Ultrasonic Gas Leak Detector designs use either simple analog filters with alarm trigger levels to cut out low frequency background noise or complicated onsite “fingerprint learn” modes to reduce background noise.
The OBSERVER-i is a Third Generation Ultrasonic Gas Leak Detector that employs Artificial Neural Network (ANN) algorithms in the detector’s advanced sound processing design to differentiate between unwanted background noise and real gas leak noise. The Artificial Neural Network uses a mathematical algorithm to search for commonality in large and complicated sets of data.
Training of the Neural Network
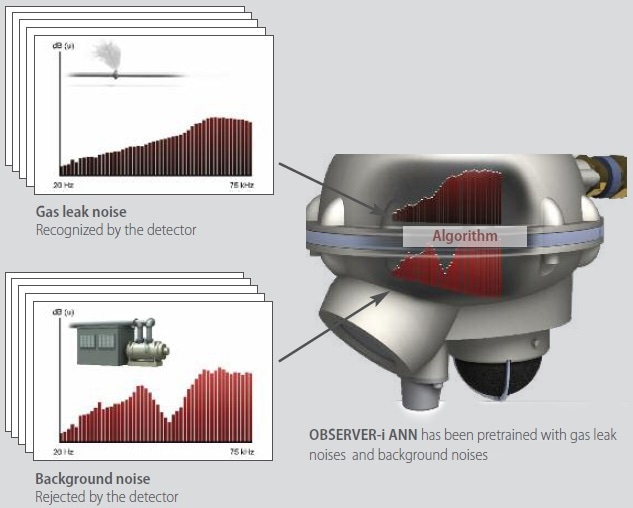
The Artificial Neural Network works very similar to how the human brain handles the constant flow of information. When one meets a person, the brain collects a large amount of visual information using the eyes and over time this significant amount of information is used to recognize this person years later or even to identify further family members. When the brain has received visual information about other family members, it can easily differentiate between family and non-family members.
In other words, the more one trains one’s brain to recognize familiarity, the better one will be able to recognize or fail to recognize a person’s face. The brain looks for familiarity and not for perfect equivalent, and so does the Artificial Neural Network. However, the Neural Network needs to be trained first like the brain.
An Ultrasonic Gas Leak Detector does not have to identify various people. It has to effectively recognize the sound signature from a gas leak, simultaneously discarding sound signatures from acoustic background noise unrelated to gas leaks.
The OBSERVER-i has pre-trained Neural Network algorithms that are an outcome of more than 10 years field experience and many acoustic data recordings from onshore and offshore facilities to develop and train the ANN algorithms. Complex onsite training approaches are not needed by the detector to adapt to specific acoustic plant conditions. Instead it performs optimally in various types of acoustical environments, immediately after installation.
Even if the background noise conditions change, the ANN algorithms will automatically compensate for that, so that no re-training will be needed.
The Three Generations of Ultrasonic Gas Leak Detectors
First Generation
First generation Ultrasonic Gas Leak Detectors make use of simple analog high pass filters to stop low frequency acoustic noise from activating the detector. Even though the detectors function well, they have a decreased detection range based on the nature of the background noise. The detection range is decreased in very noisy areas due to the need for high alarm trigger levels.

Second Generation
Second generation Ultrasonic Gas Leak Detectors use pattern recognition, where each detector in the plant is trained after installation to curb only the particular acoustic background noise the day the training took place. False alarms may ring if the background noise signature changes due to changing plant process conditions, which would result in performing a new training of the detector and lead to a change in the leak detection performance.
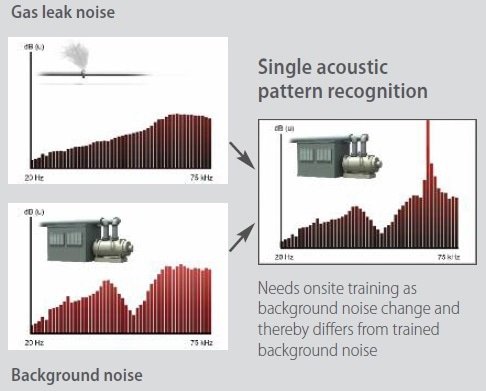
Third Generation
Third generation Ultrasonic Gas Leak Detectors make use of Artificial Neural Network Technology where the neural network algorithms are pre-trained with noise signatures from real gas leak noise and various background noise signatures (choke valves, compressors, helicopters, etc.). These Ultrasonic Gas Leak Detectors offer a combination of easy installation and operation, even in changing plant conditions and simultaneously offer an absolute market leading gas leak detection performance.
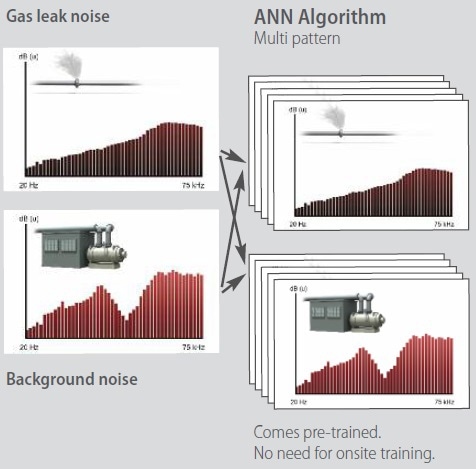
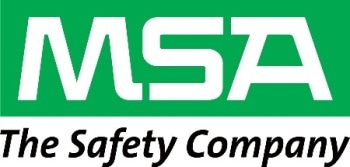
This information has been sourced, reviewed and adapted from materials provided by MSA - The Safety Company.
For more information on this source, please visit MSA - The Safety Company.