Large and complex areas filled with process equipment can face risks from toxic or combustible gas leaks, flames, and explosions. Fixed flame and gas detection systems are specifically developed and installed to protect these areas against flames and gas leaks. However, these systems can be deemed effective only if they offer a high possibility of detecting the presence of any gas and flame hazards within the monitored process areas.
Hence, it is important to determine the optimal quantity and location of gas and flame detectors in order to ensure the effectiveness of the detection system.
However, detector placement has mostly depended on common practice, previous experiences and prescriptive standards. While these approaches are not essentially incorrect, they do not provide a systematic way of assessing gas and flame under various gas release conditions, obstruction scenarios and wind conditions. Also, these conventional methods do not provide a simple means of quantifying the effectiveness of detection systems and risk reduction performance when different detector technologies, quantities and locations are deployed. Since traditional approaches have many limitations, users can find it difficult to optimize their gas and flame detection assets, or to measure the effectiveness of their existing detection methods in meeting their safety performance goals.
Flame and Gas Mapping
General Monitors’ flame and gas mapping provides an ideal solution. This tool not only helps assess gas and flame risks within a monitored process facility, but also reduces these risks towards an acceptable risk profile. In flame and gas mapping, detectors are placed in appropriate locations to obtain the best possible detection coverage. With the help of design iterations, the effects of detection technology or different detector arrangements on detection coverage are measured and evaluated, and this is stopped once the required performance target is met. The method used is based on the recommendations described in ISA's TR84.00.07 Technical Report. Once the process is completed, a mapping report that comprises of numerical estimates of detection coverage, graphical maps of residual risks and recommended detector placements is provided to the customer.
.jpg)
Figure 1. Flame and gas mapping service sequence.
.jpg)
Figure 2. Our flame and gas mapping study approach.
General Monitors’ mapping process supports the new-generation detection technologies and thus enables users to customize their detector mix to suit particular applications. These detection technologies are given in the following table:
Combustible Gas |
Toxic Gas |
Flame |
• Point Catalytic Bead |
• Electrochemical (ECC) |
• MSIR |
• Point IR |
• Solid State (MOS) |
• DFIR |
• Open Path IR |
• Photoacoustic-IR (PIR) |
• UVIR / UVIR-H2 |
• Ultrasonic |
|
• UV |
Effigy Flame and Gas Mapping 3D Software Tool
KENEXIS’ Effigy Flame and Gas Mapping 3D Software tool was used for flame and gas mapping studies. Compliant with the ISA TR84.00.07 standard, the software tool detects risk areas of flame or gas release by measuring risk likelihood through modeling. The resulting models offer a deterministic means of establishing the quantity and type of detectors required, detection coverage and detector placements offered by the installed detectors, and the remaining flame and gas risks after the installation of the detector.
Powerful modeling algorithms in the Effigy Flame and Gas Mapping 3D Software tool measure scenario and geographic-based detection coverage for flame as well as gas mapping studies. During calculations of detection coverage for gas mapping, these algorithms integrate gas detector sensitivity and hundreds of gas release and dispersion scenarios that could potentially occur in the area of study. When mapping flame detection, algorithms account for the flame detector’s sensitivity settings, field-of-vision, obstructions, radiant heat output (RHO) of the target flame and obstructed flame plumes. These modeling results are displayed by the Effigy Flame and Gas Mapping 3D Software tool in graphical color-coded coverage maps that demonstrate the level of flame and gas coverage.
Improving Gas Detection Coverage with Gas Mapping
Case study: Modeling volatile liquid hydrocarbon release from 7 pumps
.jpg)
Stage 0 analysis
- 2D gas map with no gas detectors
- Map showing initial gas risk with 0% scenario detection coverage
.jpg)
Stage 1 analysis
- 2D gas map with an initial placement of 4-point gas detectors
- Map showing reduction of gas risk with 60% scenario detection coverage
.jpg)
Stage 2 analysis
- 2D gas map with 4-point and 3 open path gas detectors
- Map showing significant reduction of gas risk with >90% scenario detection coverage
.jpg)
Stage 3 analysis
- 2D gas map with final placements of 3 open path and 9-point gas detectors
- Map showing negligible residual undetectable gas risk with >99% scenario detection coverage
.jpg)
Final stage
- 3D rendering of gas map with final detector placements
.jpg)
Improving Flame Detection Coverage with Flame Mapping
Case Study: Modeling Small Flames (1 sqft) around 7 Pumps
.jpg)
Stage 0 analysis
- 2D flame map showing undetected flames around pumps
.jpg)
Stage 1 analysis
- 2D flame map with an initial placement of 2 MSIR flame detectors
- Incipient flames at 2 pumps may be blocked from detection view
- Flame coverage for Grade A zone:
.jpg)
.jpg)
Stage 2 analysis
- 2D flame map with 3 MSIR flame detectors
- All areas around pumps are now in the view of at least 1 flame detector
- Flame coverage for Grade A zone:
.jpg)
.jpg)
.jpg)
Stage 3 analysis
- 2D flame map with final placements of 3 MSIR flame detectors
- Map showing no risk of undetected flames around pumps with >99% scenario detection coverage
.jpg)
Final stage
- 3D rendering of fire map with final flame detector placements
.jpg)
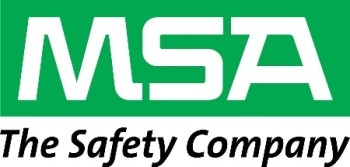
This information has been sourced, reviewed and adapted from materials provided by MSA - The Safety Company.
For more information on this source, please visit MSA - The Safety Company.