Knowing the degree of accuracy of monitoring inventory in silos, tanks, and bins is a challenging task. This article discusses why it is a difficult question to answer and what can be and cannot be expected from a level monitoring system.
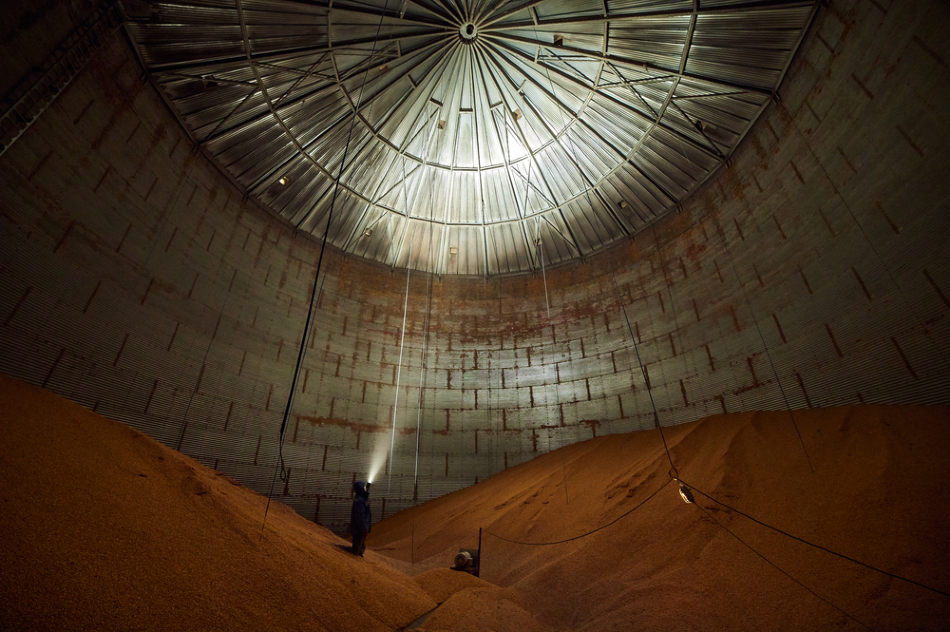
Image Credit:Shutterstock/bondart photography
Accuracy of a Single Point Inventory Measuring System
Devices such as ultrasonic level sensors, guided wave radar, bobs, and open-air radar used for level measurement measure a single point in the vessel (Figure 1). When installed properly, all these devices deliver a performance matching their printed measurement accuracy mentioned in their literature.
.jpg)
Figure 1. Single Point Inventory Measuring System
The printed measurement accuracy of a single point measurement device is actually the distance measured from the sensor placed over the top of the vessel to the surface of the material. This distance is called headroom and provides data about the available space in the bin. Nevertheless, it does not represent the accuracy of the mass or volume of the material in the bin.
Volume Calculation
The amount of three-dimensional space occupied by the material is called ‘volume.’ To calculate volume using a single point measurement device, vessel dimensions need to be accurate as inaccurate geometry can affect volume calculations by increasing the overall error. Volume calculations can also be affected by material flow, bridging, or buildup. The location of the sensor and the position of the filling and discharge points will also affect the overall accuracy of volume.
Mass Estimation
In case of volume to mass conversion, the accuracy of a single point measurement device will be further affected due to the difference in the actual value of the bulk density of the material in the bin from the literature value. This is due to the impact of attributes, including moisture content, particle size and shape, on the bulk density. There is difference in the bulk densities of the same material in the top and the bottom of the bin owing to compaction. An average bulk density needs to be established based on the actual material handled at the facility to perform mass calculations using bulk density for a specific material.
What to Expect When Using a Single Point Measurement Device
For a single point measurement device, the measured distance is highly accurate (± 0.25% of the distance measured). Nevertheless, in the case of volume calculations using level, sensor placement, the correctness and completeness of the vessel dimensions, and the position and number of filling and discharge points will influence the accuracy. A single point measuring device can provide better results in vessels that are center filled and center discharge and filled with freely and symmetrically flowing material.
Variations in bulk density will inherently cause errors in volume to mass conversion irrespective of the use of a single point or multiple point measuring device. Furthermore, the accuracy of the volume calculation will influence the accuracy of the mass estimation.
Accuracy of a Multiple-Point Inventory Measuring System
Unlike conventional single point measuring devices, a 3DLevelscanner gets measurements from different points within the silo (Figure 2). These points are utilized to calculate the volume of material in the bin. Averaging the measurement points is not done for bin volume calculation, but each point is provided with a ‘weight’ or relevancy rating. The true volume of the material in the bin is calculated using a complex algorithm. This technology considers differences that can take place throughout the topography of the material surface through measurement and mapping of the low and high points.
.jpg)
Figure 2. A 3DLevelscanner gets measurements from different points within the silo.
The 3DlevelScanner yields an accurate 3D profile of the top surface within a bin. This is useful when there are differences in the material surface owing to multiple fill and discharge points, or materials like powders that do not fill/discharge symmetrically. Like a single point measurement sensor, a 3DlevelScanner also depends on the strategic placement of the sensor and the accuracy of the vessel dimensions for volume accuracy.
The 3DlevelScanner also has inherent inaccuracy problem in volume to mass conversion owing to bulk density variables. Nevertheless, the accuracy of mass calculation will be improved due to the improved accuracy of the volume calculation. Multiple measurement points contribute a higher degree of accuracy in the 3DlevelScanner. With proper sensor placement and correct vessel geometry, volume accuracy of 3% to 5% can be expected. With good average bulk density, one can expect mass accuracy of around 5-10%.
Conclusion
With strategic placement of the sensor, a good average bulk density, and accurate vessel geometry, mass accuracy of around 8% to 15% can be expected from a single point measuring device. With proper sensor placement and correct vessel geometry, volume accuracy of 3% to 5% can be expected a multiple-point inventory measuring system. With good average bulk density, one can expect mass accuracy of around 5% to 10% from a multiple-point inventory measuring system.

This information has been sourced, reviewed and adapted from materials provided by BinMaster.
For more information on this source, please visit BinMaster.